Fluid mixers
LIQUID MIXERS
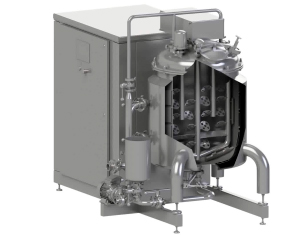
capacity
100 l, 200 l, 300 l
Mixer with a wide range of applications, mainly intended for mixing light liquids, such as shampoos, soaps, conditioners, household chemicals and car cosmetics. The specification of the liquid mixer is significantly extended due to the cold (i.e. without a heating jacket) and hot mixing technologies. We adjust the selection of mixers, pumps and equipment to the customer's needs and product specifications. Our solutions enable the introduction (suction) of raw materials directly under the mirror, avoiding air pockets and minimizing foaming, thanks to a specially designed system of nozzles and orifices mounted directly on the by-pass circulation system. The possibility of a very wide configuration will allow you to choose an economical and effective process solution.
APPLICATION:
shampoos, liquid soap, gels, conditioners, emulsions, car cosmetics, household chemicals
LIQUID MIXERS
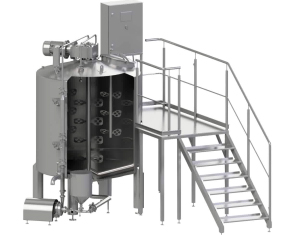
capacity
500 l, 1000 l, 2000 l, 4000 l, 5000 l
Industrial universal high performance liquid mixer for the production of liquids, shampoos, conditioners, gels, emulsions and suspensions. Apart from the traditional method of mixing with a frame agitator, a special by-pass system is used which enables flow mixing without the use of a mechanical agitator. The mixing process takes place in a special chamber mounted directly on the by-pass circuit pipe. The strong flow stream generated in this system and the negative pressure created allow the introduction of raw materials under the product mirror without the need to create a vacuum in the tank. A set of replaceable sieves and filters accelerates the digestion of materials that are difficult to dissolve or have a tendency to agglomerate. This solution is very economical and allows you to buy a fully functional mixer at an attractive price.
APPLICATION:
shampoos, liquid soap, gels, conditioners, emulsions, car cosmetics, household chemicals
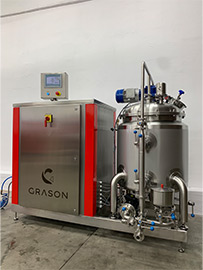
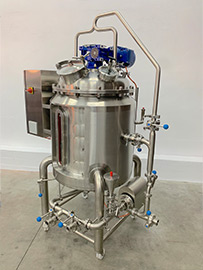
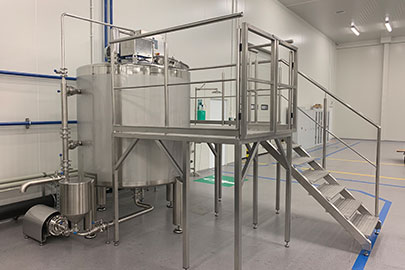
Specification and equipment
Additional options:
Control – operating panel:
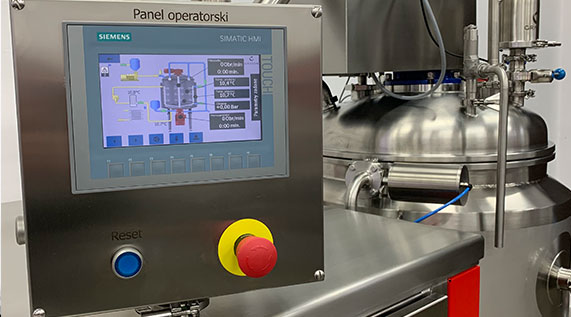
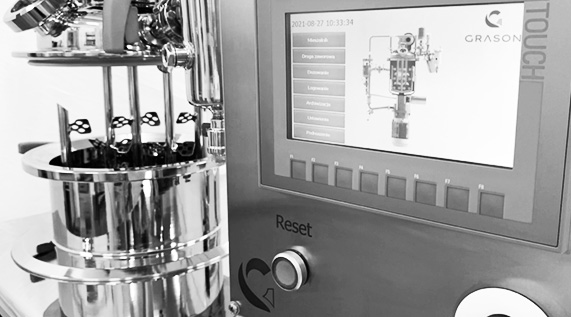
Specification and equipment
SMALL CAPACITY LIQUID MIXER | HIGH CAPACITY LIQUID MIXER | |
---|---|---|
APPLICATION: | shampoos, soaps, gels, conditioners, emulsions, suspensions, car cosmetics, household chemicals | |
OFFERED CAPACITIES IN LITERS | 100, 200, 300 | 500, 1000, 2000, 4000, 5000 |
ROTATION OF THE FRAME MIXER | 20–60 rpm | 10–40 rpm |
ROTATION OF THE HOMOGENIZING MIXER | – | – |
DRUM ROTATION RANGE | - | - |
HEIGHT OF KEEPING THE PRODUCT TEMPERATURE | - | - |
VACUUM PRESSURE | - | - |
ELECTRICAL POWER | 400 V / 50 Hz 63 A | 400 V / 50 Hz 175 A |
SERVICE AND WARRANTY
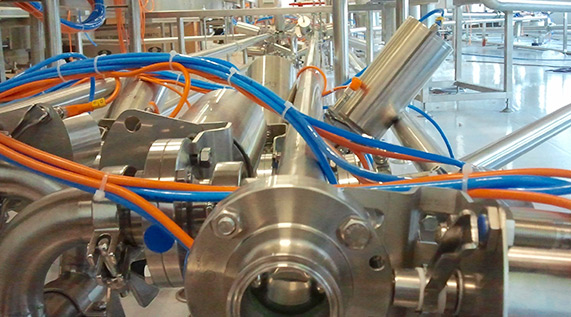